How Android Barcode Scanners Revolutionize Logistics Efficiency
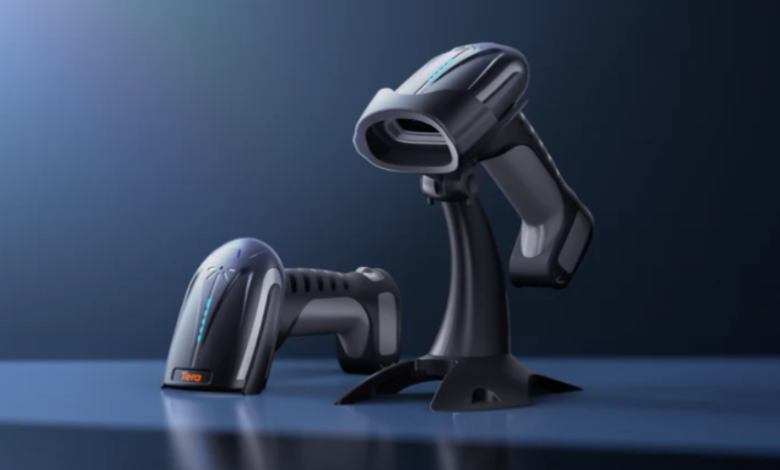
In the competitive world of logistics, speed and accuracy are not just goals; they are requirements for survival. Misplaced inventory, shipping errors, and fulfillment delays can create costly disruptions across the entire supply chain. While traditional manual tracking methods are slow and prone to human error, modern systems built on Android barcode scanners provide a path to greater efficiency and real-time operational control.
These purpose-built devices are transforming how warehouses and distribution centers manage the flow of goods. By automating data capture and integrating with management software, they empower logistics teams to work faster, smarter, and with fewer mistakes. This technological upgrade is essential for any business aiming to thrive in today’s demanding market.
The Role of Barcode Scanning in Modern Logistics
Android barcode scanners are handheld computing devices specifically designed for industrial environments. They combine robust scanning technology with powerful data processing capabilities, all running on a versatile operating system. Unlike using a standard smartphone, these devices are built for durability and are designed to connect seamlessly with a company’s core logistics software, such as a Warehouse Management System (WMS) or Enterprise Resource Planning (ERP) platform.
The primary function of these tools is to capture data quickly and accurately. Each scan provides an instant, error-free update to a central system. This capability is fundamental to modern logistics, enabling businesses to achieve a level of operational visibility that was previously impossible.
See also: Advanced Video Editing Techniques for Professionals
Key Areas of Optimization
The impact of Android barcode scanners is felt across every major function within a warehouse or distribution center. They introduce new levels of efficiency from the moment goods arrive until they are shipped to the customer.
Streamlining Receiving and Putaway
The logistics lifecycle begins at the receiving dock. With an Android scanner, workers can instantly scan barcodes on incoming shipments to verify contents against purchase orders. This process confirms that the correct items and quantities have been received, flagging any discrepancies immediately.
Once verified, the WMS can direct the worker on where to store each item. This guided ‘putaway’ process ensures goods are placed in their optimal location, improving inventory organization and making items easier to locate for future orders.
Enhancing Order Picking and Fulfillment
Fulfilling customer orders accurately and quickly is critical. Barcode scanners guide warehouse staff through the most efficient picking routes, showing them the exact location of each item. As workers retrieve a product, they scan its barcode to confirm it is the correct one.
This simple validation step dramatically reduces picking mistakes, which leads to fewer incorrect shipments and lower return rates. By removing manual cross-checks, operations become faster, and overall productivity increases.
Ensuring Accuracy in Packing and Shipping
Before a package is sealed, scanners provide a final layer of quality control. During the packing process, scanning each item verifies that the order is complete and correct. Once packed, a shipping label with its own unique barcode is generated and applied.
A final scan of the shipping label links the package to its tracking information. This gives both the logistics company and the end customer real-time visibility into the shipment’s journey, enhancing transparency and trust.
Achieving Real-Time Inventory Management
Perhaps the most significant benefit is the shift to real-time inventory management. Manual inventory counts are time-consuming and often outdated by the time they are completed. In contrast, every scan with an Android device updates inventory levels instantly.
This live data provides managers with an accurate, up-to-the-minute view of stock levels. It helps prevent stockouts of popular items and reduces the cost of holding excess inventory, enabling smarter purchasing and sales decisions.
The Advantages of Android-Based Systems
The use of an Android operating system brings additional benefits that traditional single-purpose scanners cannot match. This platform provides the flexibility needed to adapt to evolving operational demands.
Versatility and Multi-Functionality
A key advantage of Android-based scanners is that they are not limited to a single task. A single device can be used for scanning, communicating with team members, taking photos of damaged goods, and running various logistics applications. This consolidation of tools simplifies a worker’s load and streamlines different tasks into one workflow.
Seamless Integration and Data Management
These devices are designed for constant connectivity. With Wi-Fi and cellular capabilities, they sync data instantly, ensuring that information in the WMS is always current. For operations in areas with poor connectivity, many devices can store data offline and automatically upload it once a connection is re-established.
This seamless data flow is crucial for modern logistics. The hardware that supports these advanced software functions must be reliable and powerful. Companies are now looking for devices that can handle high-volume scanning, operate for long shifts, and withstand the rigors of a warehouse environment. High-performance tera barcode scanners are an excellent example of this new generation of hardware, built to power the sophisticated applications that drive today’s logistics.
Cost-Effectiveness and Scalability
Compared to older, proprietary scanning systems, Android-based solutions can offer a more cost-effective way to equip a workforce. The familiar interface reduces training time, and the ability to deploy new applications via software updates makes the technology highly scalable. Companies can easily expand their device fleet during peak seasons without a massive investment in specialized hardware.